热塑性碳纤维层压板未来可以采用超快进给钻孔方式
航空航天和汽车制造是现代工业领域里最能体现工业能力和产业链完成度的两个行业,其中涉及到的技术和材料数不胜数。碳纤维及复合材料是当下工业生产中非常火热的一种新型材料,凭借出色的力学性能获得了较好的应用。在实际应用中,碳纤维作为增强体材料,与不同的基体材料融合,可以被加工成各种外形的工业零部件,其中有部分就可以应用于航空航天和汽车制造领域。
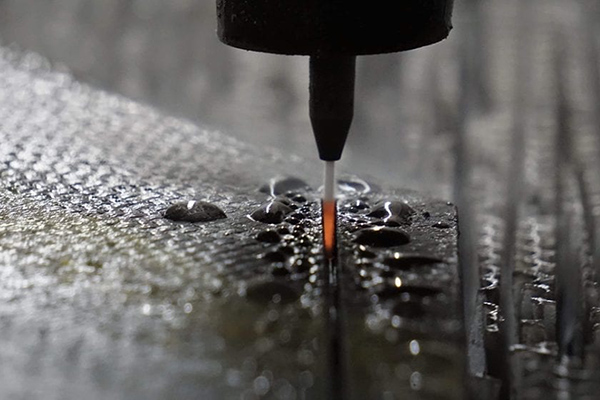
目前主流的热固性碳纤维,以及未来更有优势的热塑性碳纤维,都被认为是难以超越的高性能复合材料。但将这些碳纤维复合材料加工成制品有一定的难度,其中需要各种设备和机械的配合,打孔、裁切、镂空等属于基本操作。但不要轻视这些基本的加工过程,加工操作对于碳纤维制品的性能同样有着至关重要的联系。本文引用国际专业论文知识,介绍超快进给钻孔这种加工方式,并与超声波振动和磨料水射流这两种加工方式做一些比较。

热塑性碳纤维(CF/PA6)层压板的3种钻孔方式
1、超快进给钻孔(UFFD):切削热和摩擦热会导致热塑性基体的熔化,影响钻孔效率和效果。为了研究超快进给钻孔方式的实际效果,将热塑性碳纤维层压板固定,选用3000、5000和7000mm/min的进给速度,利用三分量测力计测量。
2、超声波振动钻孔(UVD):将压电晶体振荡器安装在设备上,提供70kHz的恒定频率,观测超声波振动在对热塑性碳纤维层压板钻孔的实际效果。
3、磨料水射流钻孔(AWJ):磨料水射流加工是目前热固性碳纤维制品切割的主流方式,将水射流轨迹设计成圆形,施加一定的水压,对热塑性碳纤维层压板进行钻孔处理,观测实际效果。

超快进给钻孔方式实际效果展示
1、钻孔效果对比:3000mm/min超快进给速度和50mm/min低进给速度比较下,前者切削完成速度更快,排出少量切屑,钻孔附近没有毛刺残留,后者在钻头穿透前层压板有明显变形,切屑残留较多,孔周围有冠状毛刺。3000mm/min的推力峰值是50mm/min时的6倍,接近22N,钻孔时间却只有后者的1/60,钻孔效率大幅提升,同时钻孔的质量也更好。

2、分层和毛刺情况:利用3D测量显微镜观察发现,分层和毛刺出现与钻孔的入口方向,以20μm为分界线进行区分。当进给速度为3000mm/min时,主轴转速无论高低都没有出现分层。当进给速度高于3000mm/min,主轴转速超过20000min-1时,分层体积随进给率的提升而增加,这是因为高进给速度下的推力更大。

另外主轴转速越高,出现的毛刺体积也就越小。通过多次实验发现,进给速度为3000mm/min,主轴转速为20000min-1时,不会出现分层的问题,同时保持较小的毛刺体积,整体的钻孔效果更好。

3、与其他两种钻孔方式的对比:为了更好对比钻孔效果,实验中观测了每种钻孔方式的微观图像画面。超快进给钻孔(UFFD)孔壁处每一层碳纤维清晰可见,而超声波振动钻孔(UVD)和磨料水射流钻孔(AWJ)的孔壁有被熔化的基体覆盖的情况,表面较为模糊。放大微观图像后,磨料水射流钻孔(AWJ)孔壁处有明显的尼龙线扩散开,相较之下超快进给钻孔(UFFD)的孔边缘质量更好。按照孔表面质量、形状精度和加工时间来比较,超快进给钻孔(UFFD)是一种更有前景的热塑性碳纤维层压板的钻孔方式。

给热塑性碳纤维板开孔是一种较为基础的加工方式,这样就可以与其他的工业零部件稳定的连接起来,发挥更大的商用价值。目前热塑性碳纤维复合材料的大范围应用还处于起步阶段,热塑性碳纤维复合材料单向带的制备难度较大,从源头上限制了该型复合材料的应用。智上新材料作为国内少数几家可以独立完成连续碳纤维热塑性复合材料单向带制备的企业,认为热塑性碳纤维的发展还需要从基础层面出发,技术进步才是解决问题的首要条件。
本文涉及论文来源:https://doi.org/10.1016/j.procir.2015.08.074
上一篇:环境因素会影响热塑性CF/PEKK复合材料的性能吗?
下一篇:没有了