现阶段可实操的5种热塑性碳纤维复合材料成型工艺
热塑性碳纤维复合材料是指由碳纤维与热塑性树脂融合后形成的产物,不同形态的碳纤维和不同类型的热塑性树脂的融合难度存在巨大差异,融合后的性能差距也存在较大的区别。当下以连续碳纤维与热塑性聚醚醚酮树脂形成的复合材料的性能较出色,且该复合材料的制备具备批量生产的可能。
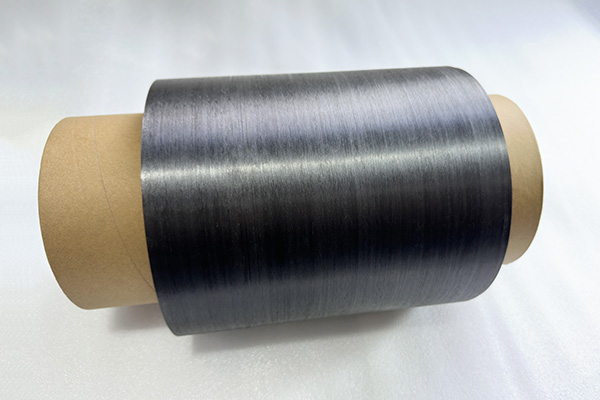
热塑性碳纤维复合材料从理论到实践的过程中,制备复合材料是难度较高的一个环节,而另外一个环节是如果将复合材料较为简便的制成各种外形的零部件,同时保持物理结构上的完整与机械性能上的优势。想要解决以上2个环节存在的问题,不仅需要理论研究,而且实践测试必不可少,现阶段有哪些被证实可行的加工成型方案?智上新材料带大家了解一下。
现阶段可实操的5种热塑性碳纤维复合材料成型工艺
1、熔融浸渍成型
熔融浸渍是制备结晶性聚合物浸渍带的最佳选择,从熔融浸渍装置的喂丝架引出单向、平行、固定张力的纤维丝束,送入熔融浸渍槽中浸渍热塑性树脂,经过高温炉和热压辊压制成预浸带后,由收卷系统绕成卷。熔融浸渍工艺的核心是让纤维束最大程度地分散,并使得纤维束内部得到充分浸润。
在该方法中,达到熔融状态的树脂在一定压力下对处于分散状态的纤维束进行浸渍,理想状态下纤维束内部将得到充分浸润,最后冷却得到预浸料或预浸纤维条。熔融浸渍工艺简单,过程中基本不产生挥发性气体,同时能精确地控制预浸料的纤维含量;但在高黏度树脂体系下浸渍效果不佳,纤维展开分散较为不易。
实验发现,将碳纤维穿过自行设计并安装于单螺杆挤出机上的浸渍机头后,向进料斗加入与抗氧剂混合后的PA66树脂,进行熔融塑化,从而对连续碳纤维进行包覆、浸渍,制得不同碳纤维含量的CF/PA66预浸料单向带。
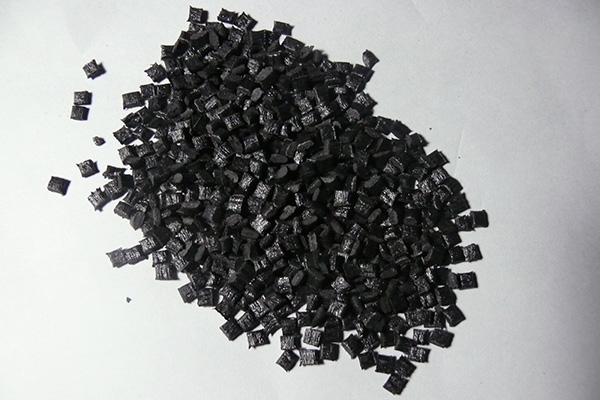
2、挤出-注射成型
目前短切碳纤维(SCF)复合材料成型工艺以挤出-注射成型为主。在成型过程中,短切碳纤维复合材料熔体的流变性能主要受到加工温度和剪切应力的影响。加工温度低于临界值时,熔体的表观黏度随加工温度升高而降低;超过临界值时,表观黏度不再随加工温度发生明显变化,显示出牛顿流体的特性,此时适宜复合材料的成型与加工。切主要影响熔体的黏流活化能,剪切应力越小,黏流活化能越大。
将PA66、集束性短切碳纤维、相容剂、耐磨助剂、抗氧剂等加入到高速混合机中,在室温下混合;再将混合好的原料通过双螺杆挤出机熔融共混、挤出,经水冷、干燥后进行切粒;将制备好的粒料烘干后,通过注射成型制得了集束性SCF增强PA66复合材料。
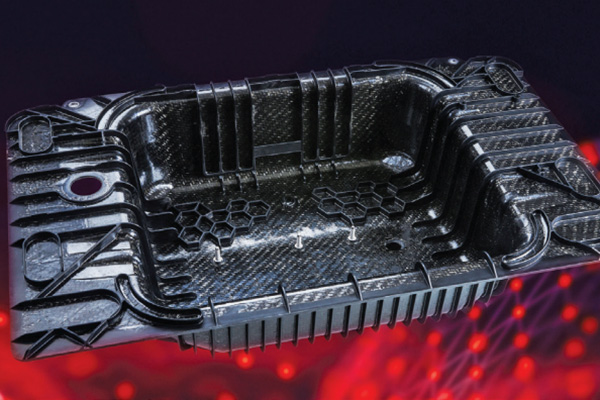
3、模压成型
模压成型是将裁好的热塑性碳纤维复合材料预浸料片材或含有碳纤维的混合坯料放入模具中,随后将热塑性树脂加热到熔点或黏流温度以上,使树脂熔融、流动、浸渍和包裹增强纤维,并通过界面紧密地结合在一起,最后冷却定形的一种成型方法。该方法具有操作简单、生产效率高、能耗及成本均较低等优点。
实验发现,采用连续碳纤维增强热塑性复合材料可直接在线模压成型,工艺特点是全过程熔体只加热一次,保留了连续碳纤维的形态下直接成型,最大程度地保留了碳纤维在产品中的长度,而且生产效率高、产品成型容易、生产成本较低,未来可生产汽车用发动机阀盖、脚踏板、齿轮罩盖等对尺寸及性能要求严格的零部件。
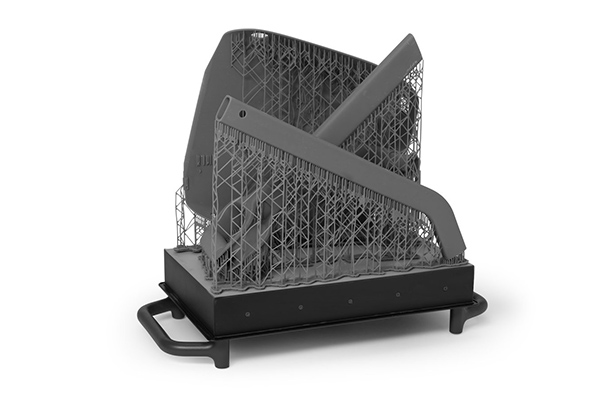
4、3D打印成型
3D打印成型技术具有设计自由、可以直接快速打印传统方法难以打印的复杂构件的优势。熔融沉积成型(FDM)是一种简单的3D打印工艺,它通过加热挤出头的熔融塑料纤维,并将熔料铺叠在平台的单层上,每个铺层都与前一个铺层互相粘接,最终冷却硬化成型。使用FDM打印的模型精确、工艺可靠;但是在打印形状凸出的模型时,则需要额外的支撑结构,否则会很容易塌陷或者断裂。
3D打印成型对复合材料的利用率高,能够做到较高的精度和复杂程度,可以打印传统方法难以打印的复杂构件,而且它从数据模型到构件成型的时间短,适合新产品的开发和小批量零件的生产。
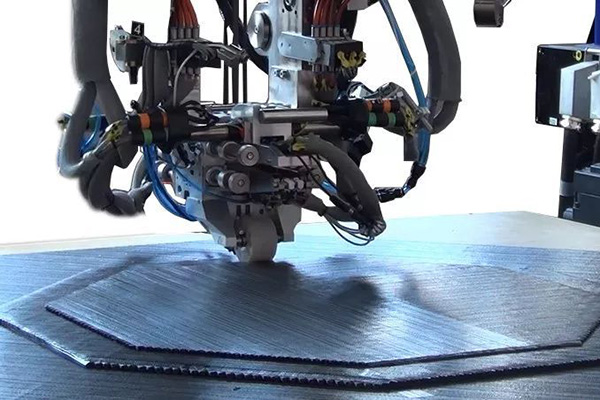
5、自动铺放成型
自动铺带技术是一种增材制造工艺,通过带有特殊加热装置的铺丝或铺带设备进行定位、铺叠和原位固化,在构件厚度方向上逐层增加,最终达到设计的尺寸、完成零件的制造。该技术多用于航空航天领域,适合生产复杂形状双曲面构件。这种成型工艺具有生产效率高、自动化程度高、易于数字化设计等优点。
自动铺带系统通常由预浸料供料盘、自动铺带头、构件模具、数控系统、计算机辅助设计(CAD)软件等组成。系统工作时,将复合材料预浸带放入铺带头中,由多轴机械臂控制铺带位置,一组滚轮将预浸带导出,经过工艺加热后在压辊的作用下铺放到模具上或上一层已铺好的材料上,最后由切割刀将预浸带切断,这样就完成了一次铺带。
与手工铺叠成型相比,自动铺放成型效率明显提高、废料量更少、尺寸精度更高、内应力更低,是未来大型构件制造的发展方向。
碳纤维复合材料成型工艺的改进过程,贯穿整个碳纤维产业的发展。不管是当下主流的热固性碳纤维,还是未来具备较大潜力的热塑性碳纤维,都会因为成型工艺的改善,从而得到产能和性能强度的提升。随着对碳纤维复合材料研究的深入,更智能化的成型工艺必然会出现,碳纤维产业的发展终将迎来更好的明天,智上新材料始终坚信这一点。